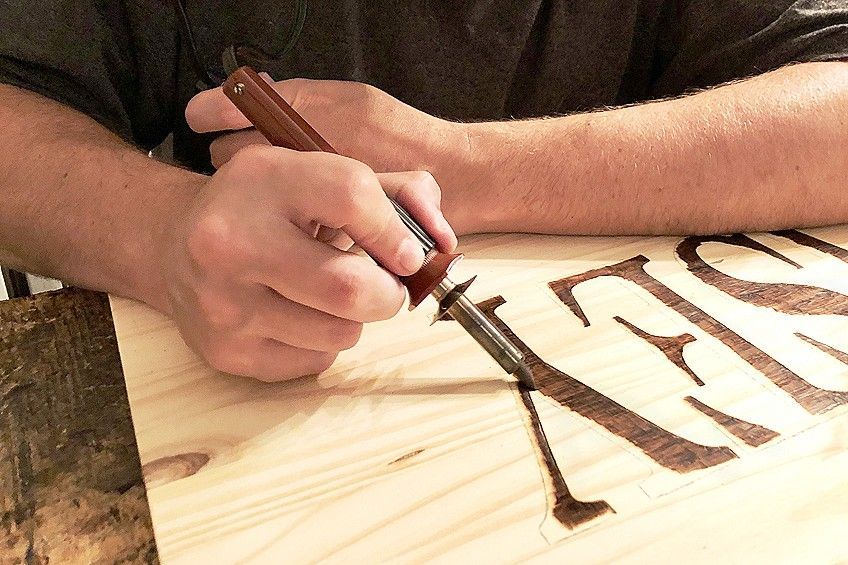
If you're interested in creating beautiful, custom pieces for your home, you may be interested in learning more about pyrography on cedar. This ancient art involves the burning of intricate designs and ornaments into wood. It dates back to 17th century. The resultant burn marks create beautiful dark designs. You can also include landscapes and portraits. This technique has been around for centuries, and is a popular choice for home decor.
Yoko sugi ban
In Japan's 18th century, shou sugiban is a method that preserves wood by charring its surfaces. This creates a rich charcoal-black color on the wood's exterior, which can also give it an Alligator skin or cracked appearance. The Japanese cedar is the most popular wood for its rustic, traditional look. However, other wood species can be used with different degrees of success. The wood will be protected from future damage through controlled charring. This is an excellent preservation technique.
Shau sugi ban
The method of removing char is the most noticeable difference between traditional sanding and shou-sugi ban. Woodworkers who use shou sugi ban sandpaper or wire brushes to remove the charred layer on the top layer of the wood are able to scrape it off with wire brushes. Either way, you want to scrape away enough char to reveal the brownish black color beneath. You will see a pattern that resembles an alligator skin. To remove excess char, sanding is required.
Shau sugi ban on cedar
Although the wood finish of shou shugi ban on pyrography looks great, it has many practical implications. You can track pieces of charred wooden wood throughout a building. Additionally, they can be inhaled easily by those who live within the treated space. To combat this problem, pyrographers are beginning to use propane torch in addition to the traditional wood-burning method. Here is a look at the differences between the two styles.
Yaki Sugi Ban on Basswood
Yakisugi ban, a Japanese technique which has been used for centuries, is an excellent way to add beauty and longevity to wood. Though sometimes referred to as Shou sugi ban, this process involves charring the surface of wood to create a beautiful pattern. This technique is so popular in Japan, that cedar is used to make many shousugi ban projects. Satoshi, the operations director for a Japanese woodworking business, discusses why shou suugi ban is so popular, and what it means for woodworkers.
Yaki sugi bans blue stain pins
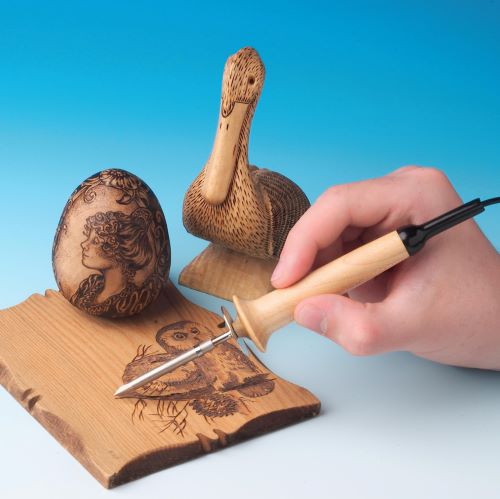
This process, also called shou sugiban, preserves wood by using fire. For shou-sugi ban, cedar was traditionally used. However, other woods are possible. Although cedar is the preferred wood for this method, yakisugi could be applied to maple, oak, or birch. Traditional Japanese craftspeople are particularly fond of this technique.
Shau sugi ban on basswood
Charring cedar wood gives it a rich, dark black color with distinctive crackled edges. Cedar is naturally water-resistant and repels pests. However, the charred surface has sculpting qualities. There are two options for charred wood: untreated or reclaimed. A cedar panel can also be treated to achieve a subtler burnt wood finish.
Shau sugi ban on jelutong
Shou sugi ban on wood pyrography has many benefits. First, it enhances the wood's natural patterns. Charred wood is also more durable due to the thicker carbon layer. This is largely dependent on the timber species and the environment in which it is applied. If you're looking for an environmentally friendly way to treat wood, shou sugi ban is definitely worth trying.
FAQ
What is the difference between a hobbyist or a professional woodworker, and how can you tell?
Hobbyists are passionate about making things from wood, while professionals tend to be more focused on the quality and craftsmanship of their work. Hobbyists usually take pride in their creations and often share them with friends and family. Professionals will spend hours researching designs and then begin to create a project. They'll pay great attention to details, from choosing the most suitable materials to finishing the work perfectly.
What type of wood should I choose?
The most commonly used woods for woodworking are oak, maple, cherry. Each type of wood has unique characteristics that affect the look and feel of the final product. Oak is a darker wood and tends to be more durable than other types. Birch is light and soft, while mahogany can be heavier and more dense. You can also choose between solid wood and veneers. Veneers consist of thin sheets made from wood and glued together to form a single layer.
How can I learn basic skills in woodworking?
Building a bench is a great way to get started in furniture building. This project can be done with any kind of wood that you have at home. If you don't know what kind of wood to use, then go ahead and buy some cheap pine boards from Home Depot or Lowes. Once you have built your bench, you will need to sand it off and then finish it with a stain/varnish.
Do you have any suggestions for starting a woodworking shop?
It's not easy to start your own woodworking business. You won't mind working hard if your hobby is something you love. Plus, you'll probably enjoy the challenge of running your own business.
One thing to keep in mind when launching a new venture is that you might encounter unexpected problems along the way. For instance, you might run out of money unexpectedly. You might find customers not willing to pay the amount you expected. You must be ready to deal with such situations in order to survive.
A good tip is to open a separate bank account for your business. You will always know how much money you have coming in.
Where can I start woodworking?
It is best to actually build furniture to learn how to make it. While you will need tools and make mistakes, you will eventually master the art of building furniture.
You should first choose the project you wish to complete. It can be something as simple and small as a box, or large-scale as an entertainment center. Once you have chosen a project, locate a local woodworker who is skilled in this kind of work. Ask the local woodworker for help in deciding what tools and where to get them. Ask if you can find someone who does this kind work.
Statistics
- In 2014, there were just over 237,000 jobs for all woodworkers, with other wood product manufacturing employing 23 percent; wood kitchen cabinets and countertop manufacturing employing 21 percent. (theartcareerproject.com)
- The U.S. Bureau of Labor Statistics (BLS) estimates that the number of jobs for woodworkers will decline by 4% between 2019 and 2029. (indeed.com)
- The best-paid 10 percent make $76,000, while the lowest-paid 10 percent make $34,000. (zippia.com)
- Overall employment of woodworkers is projected to grow 8 percent from 2020 to 2030, about as fast as the average for all occupations. (bls.gov)
External Links
How To
How to join wood without using nails
Woodworking is an enjoyable hobby. Woodworking can be a fun hobby because you can work with your hands to make useful objects from wood. Sometimes you may want to join two pieces together of wood without using nails. This article will teach you how to do this to keep your woodwork projects looking great.
You will first need to trim the edges of your wood pieces before joining them. Avoid leaving sharp edges that could lead to problems later. After you have completed this step, you are ready to glue your boards together.
If you're working with hardwood, you should only apply glue to one side. For softwoods like cedar and pine, glue should be applied to both sides. Once you have applied the glue, press down on the boards until they are fully attached. After applying the glue, let dry the boards before proceeding to the next stage.
After you have glued the boards together, drill holes in the joints where you intend to place screws. These holes will differ depending on the type and size of screw you are using. For example, if you intend to use 1/2-inch wood screws, you need to drill a hole that is at most 3/4 inches deep.
Once you have drilled your holes you will need to drive the screws through each joint and into the backside. Don't hit the board's surface. You could damage the finish. Don't drive the screws too far into the end. This will prevent splitting the wood's end grain.
After your project is completed, you will need to protect it from the weather. You can either cover the entire furniture or just the top. You want it to last years, so you can use any product. Some examples include oil-based varnishes, polyurethane, shellac, lacquer, etc.
These products are available at most home improvement stores. It is important to ensure that you purchase the correct product for the job. Keep in mind that certain finishes can be toxic and should not be used indoors. Always wear protective gear when handling any of these finishes.