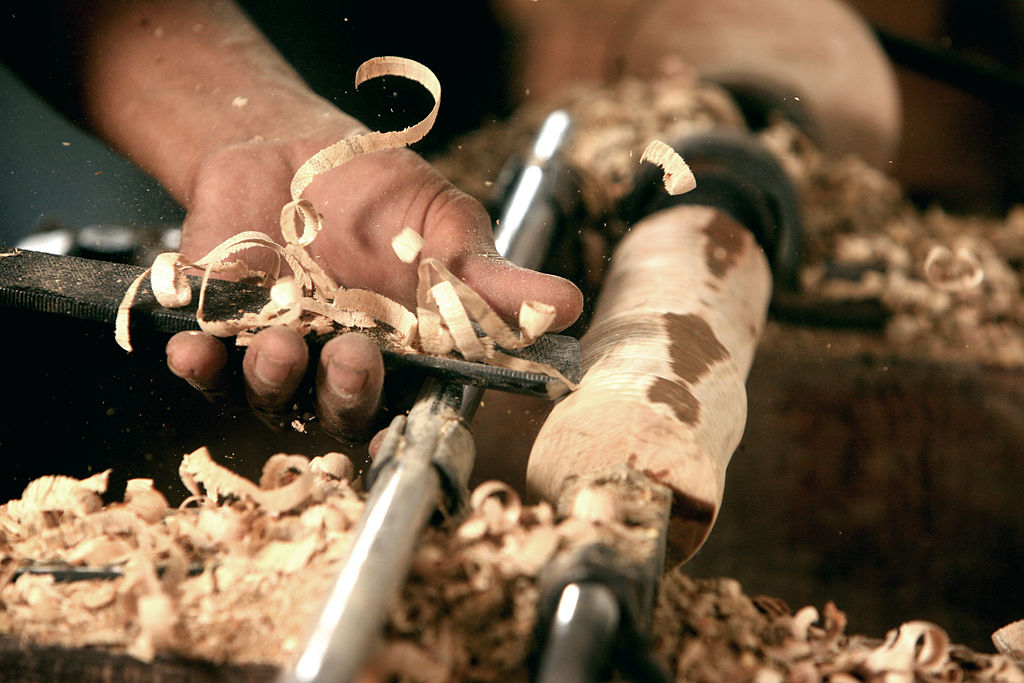
Philip Moulthrop began turning wooden in 1979. He learned his craft from his dad, Ed Moulthrop. Using a hand-forged lathe and chain saw, he roughs out the green sections of trees from southeastern regions. He then refines the bowl on the lathe, finishing it with several coats of finish. The whole process can take between four months and a year. Once the process is complete, the bowls can then be purchased or given away as gifts.
Philip Moulthrop
Phillip Moulthrop's bowl is made from red leopard maple. The process of wood turning, which he developed, has been a family tradition for three generations. Philip Moulthrop has made bowls for several notable museums and private collections. Here are some their most iconic pieces. Read on for more information on this talented artist.
Philip Moulthrop, an American painter, was born in 1947. In his 20s, he studied general arts and soon discovered a passion for woodworking. He purchased his first lathe when he was 16 years old and gradually increased his equipment. He was an innovator in his field, creating beautiful turned vessels that were well-received by the art community and the United States president. His work was soon recognized and he started selling his pieces at local craft fairs and galleries. He also began to receive international recognition.
Matt Moulthrop
The Matt Moulthrop Boulbows are a fine example of Georgia’s rich wood-turning heritage. The artist was born in Atlanta. He earned his BA and MBA at Georgia Tech. While he did spend a few years in the 9-to-5 industry, he never lost passion for turning wood. In fact, he received recognition nationally for his bowls. His works are shown at the ASU Art Museum (the Carter Center) and Racine Art Museum (the Racine Art Museum).
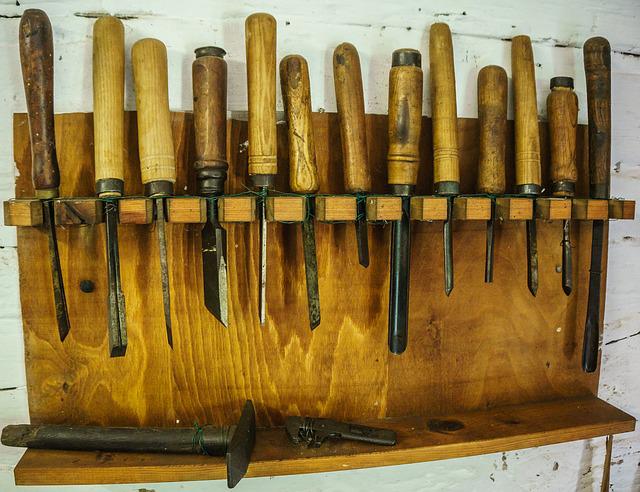
The Moulthrops have been recognized as world-class wood-turners, with works placed in prominent collections in the United States and abroad. Moulthrop pieces can be found in the Renwick Gallery of the National Museum of American Art. Collectors all over the world collect his bowls. During a Smithsonian photo shoot, the bowl maker gave each photographer a signed copy.
Ed Moulthrop
Moulthrop began to turn bowls around 1970s. Soon after, he received a scholarship at Princeton University to study architectural design. Moulthrop spent a year in Vietnam and then resigned as an architect to pursue woodturning. His large-scale, turned bowls are internationally recognized and can be found in museums like the Museum of Arts and Design in New York and the White House Collection of American Crafts. These bowls can be made from domestic woods or polished to a crystal clear finish.
This rare Ed Moulthrop bowl is nine inches in diameter by fourteen inches high and made of wild cherry. These wood bowls will be available for purchase at Gump's San Francisco. There are many other pieces of Ed Moulthrop's wooden bowls on display. The best way to learn about the artist's work is to visit the exhibition. He also publishes a beautiful catalogue of his work. Although it is possible for you to buy the bowls from museums it is much better to see his studio.
The Eagle & Phenix Dam Series
This limited edition series moulthrop bowls is made from wood from the Eagle & Phenix Dam. It's a series that was once located in Columbus, Georgia. The bowls contain traces of history and are handcrafted by local artists Matt and Philip Moulthrop. They are available to bid during regular museum hours. Additionally, a portion will be offered for sale live.
The Moulthrop family has contributed to the growth of wood-turned bowls in Georgia. Three generations of Moulthrop families have been turning bowls over fifty years. The museum is proud of their works. Many of these pieces are highly prized for their large size and smooth, polished surfaces. His mosaic bowl technique, which involves glueing thin branches to a shaped bowl with thin branches, is featured in the exhibit.
Matt Moulthrop’s work
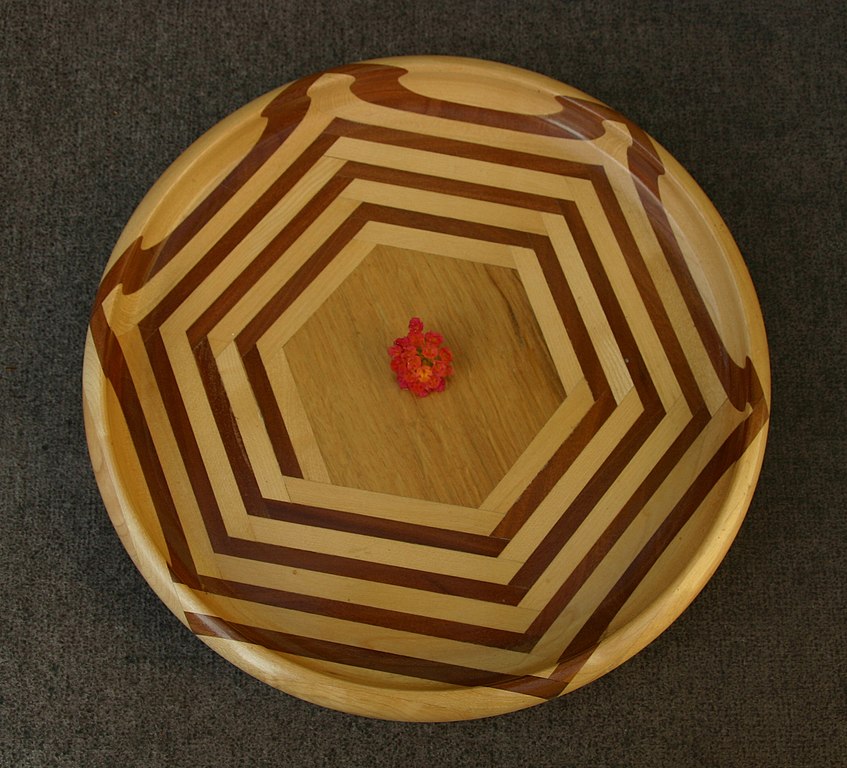
Matt Moulthrop is the son of Philip Moulthrop and Ed Moulthrop. He grew up woodturning. He was taught by his father at an early age, and his passion for woodworking grew. Matt pursued a degree in business administration at Georgia Tech after earning his BA from the University of Georgia. He is the third generation to create wooden vessels. His work is included in numerous art institutions, including ASU Art Museum and Carter Center. He is currently working with commemorative pieces to mark the 100th anniversary for Georgia Tech Alumni Association.
Georgia is not home to the wood he turns. To find wood that is not common, he travels around the world. He works with tools and a hand-forged turning lathe to make unique pieces from trees from all around the world. His wood pieces are made from wood taken from both Southeast and exotic places such as underwater forests or volcanoes. If you are a fan of his work, be sure to check it out!
FAQ
Is there a way to start my own woodworking company?
It is difficult to start your own woodworking company. There are many laws and regulations you need to be aware of. But, this doesn't mean you need to go through all of the trouble of setting up your business. Many people prefer to join existing companies. This will allow you to avoid paying membership fees and taxes.
Can I succeed in woodworking if I'm a genius?
No. Woodworking does not require any special skills. You can create beautiful pieces of art by learning how to use simple power tools.
Is there anything else I should know about woodworking?
It is easy to underestimate how much work it takes to make furniture. Finding the right wood for the project is the hardest part. There are so many varieties of wood available that choosing one can be difficult.
Another problem is that not all wood has uniform properties. Wooden can split or crack, while some woods may warp. These things should be considered before you buy wood.
How often should I buy new supplies?
Over time, you may need to replace your tools. Sharpening hand tools is a must. You'll also need to replace parts if you use power tools. You can spread your purchases over a number of months to avoid spending too much.
How do I get started with woodworking?
It is best to actually build furniture to learn how to make it. While you will need tools, mistakes are inevitable, but you will learn the ropes if you persevere.
First, choose a project you would like to complete. It can be something as simple and small as a box, or large-scale as an entertainment center. Once you've settled on a project find a local skilled woodworker. Ask them for their advice about the tools and where they can be found. It's possible to ask your friend if they do this type of work.
Statistics
- Average lumber prices rose about 600 percent between April 2020 and May 2021. (familyhandyman.com)
- Overall employment of woodworkers is projected to grow 8 percent from 2020 to 2030, about as fast as the average for all occupations. (bls.gov)
- Woodworkers on the lower end of that spectrum, the bottom 10% to be exact, make roughly $24,000 a year, while the top 10% makes $108,000. (zippia.com)
- The best-paid 10 percent make $76,000, while the lowest-paid 10 percent make $34,000. (zippia.com)
External Links
How To
How to make wooden joints
This tutorial will demonstrate how to join two pieces together of wood. We will use the "pockethole joint," which means that we drill holes in the wooden pieces and then glue them together. If your wood is straight and flat, this method will work well. You might consider dowel joinery if your wood isn’t straight or flat. Here are the steps
-
Drill Pocket Hole Joints. Start by measuring and marking the spot where the pocket hole joint will be placed. With a handheld drill machine or jig saw, drill 3/4-inch deep holes in the ends of each piece.
-
Sand Smooth. The wood's edges can be sanded to prevent splitting.
-
Glue both sides together. Apply glue to both ends of the wood. Let the wood sit for 5 minutes, then clamp it together.
-
Secure the pieces together. After the glue has dried properly, clamp the pieces together to make sure they are flush.
-
Trim Joinery. Trimming the joinery after glue has completely dried.
Be sure to leave enough space between each piece so that they can be turned inside-out.