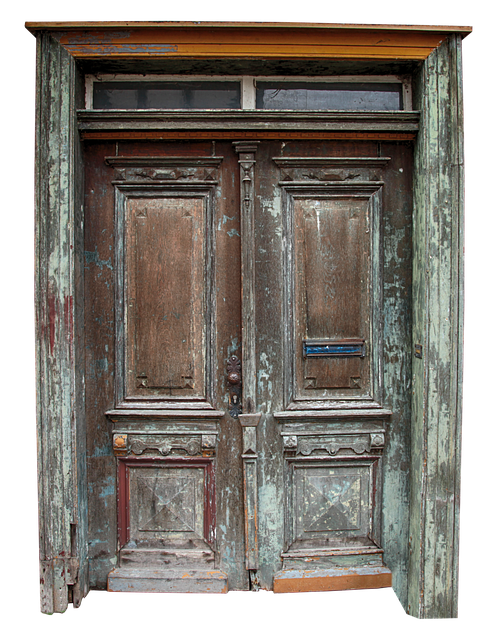
Wood carving tools with sharp edges will enhance your enjoyment. Here are some methods that you can use to sharpen your wooden carving tools. Sharp edges are more durable and will last for a longer time than dull ones. Sharp edges are more efficient and allow you to use your tools more effectively. Sharp edges make carving easier and ensure maximum cutting performance. Below are three ways to sharpen wood carving tools. Read on to learn more. - How to sharpen a sharpening stones.
Sharp edges make carving more enjoyable
In addition to sharp tools, the best carving experience is achieved by using tools with razor-sharp edges. Sharp tools require less effort and provide more control during carving. Also, a blade that has been sharply cut leaves a smooth surface. For a successful carving job, sharp tools are vital. For optimum results, hone your carving tools regularly. Regular sharpening will keep your carving tools sharp and make it easier.
Although sharp edges are a pleasure to carve, they can cause blisters. Wood's texture is natural and will not be smoothened with regular handling. While blisters can eventually heal into calluses (which is often painful and time-consuming), this process can take a while. You can try changing the way you hold your carving tools to reduce blisters. It will take practice, but it is worth it.
Use a sharpening knife and a fine grain stone to sharpen your knives. Make sure to inspect the edge for damage. Chips around the edge will require more intensive grinding. An edge that is dull may need minimal grinding with a finer grinder. Finally, you can test the knife with a piece of paper or rope. A sharpening stone may not be necessary if the knife is dulled for a while.
Common techniques for sharpening wooden carving tools
There are many methods to sharpen wood carving tools. There are several options for sharpening wood carving tools. Oil stones need oil to be applied to the stone's surface in order to prevent metal particles embedding into the surface. Both ceramic and diamond stones don’t require oil, making them ideal for sharpening wood carving tools made of carbide. This article will discuss the common techniques of sharpening wood carving tools.
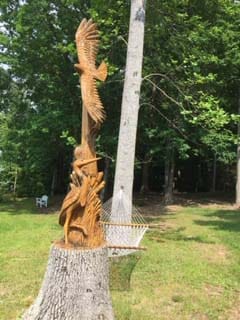
The leather strop is used to remove the wire from a blade's edge and polish it. Although leather strops can be used with all tools, some carvers prefer using a textured one. A flat leather strap is ideal for straight tools and the outside edge of gouges. If you're serious about your work, it might be worth investing in a leather strap with grooves.
Bench chisels have been sharpened traditionally at a 25-degree angle, with a secondary bevel of 5 degrees. Modern alloys can't be used with these angles and may break. You will need to increase the angle of your bevel. This will require more force, but you'll have less control. Block planes are sharpened at a twenty-degree angle.
A sharpening stone is used
A sharpening knife is a tool that can be used for wood carving. The stone's crystalline form contains grit. This mineral is hardier than steel and has sharp edges. A lubricant is required to help the stone cut and prevent metal particles becoming embedded. When your tool has been sharpened to a point that is sharp, it will be easier to use it to cut wood without resistance. The strop, which is typically made of leather, polishes the edge and removes the burr.
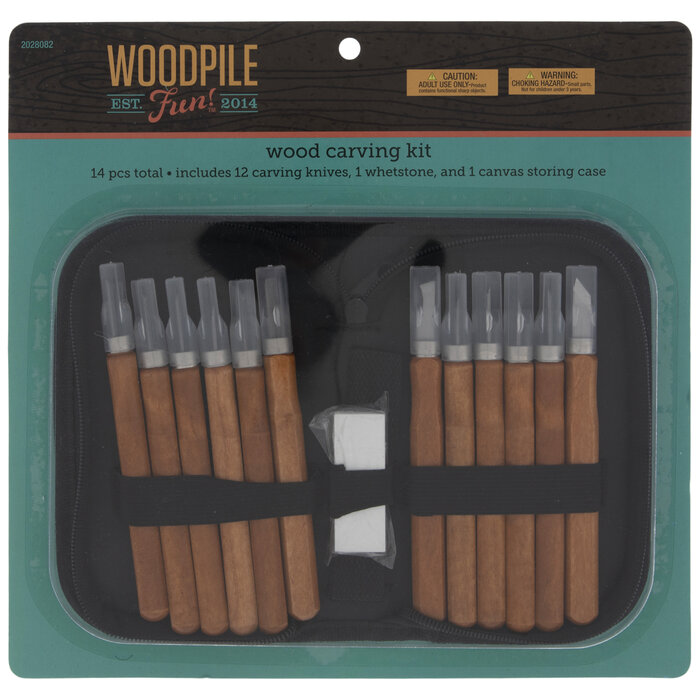
There are many different types of sharpening rocks on the marketplace. Some of them are oilstones, waterstones, and ceramic stones. The oil stones use oil as a lubricant to avoid fine metal particles from burying themselves in the stone surface. Both ceramic and diamond stones don't require any lubricants. They both work well in sharpening the carbide wood carving instruments.
The Sentima sharpening stone is a great example of a quality sharpening system. Both a coarse and fine corundum stone are featured in this sharpening system. This material is consistent in grain, which makes it easy to cut and gives it a smooth finish. Its unique design is easy to clean. The sharpening mechanism is made of durable materials, and it will last many years without deteriorating in quality.
FAQ
How can I tell what kind of wood I am working with?
Always check the label before purchasing wood. It should have information about the wood species as well its moisture content and whether any preservatives were used.
What would be your first step in woodworking?
Start with softwoods, such as pine or poplar. After you are comfortable with the softwoods, move to hardwood.
How do I organize my shop?
The first step toward keeping your workshop clean and organized is to set aside a designated area for storing tools. Make sure your tools are clean and free of debris and dust so they can be used properly. You can hang tools and accessories with pegboard hooks.
How much should a skilled woodworker earn per hour?
Hourly rates for professional woodworkers vary depending on many factors such as skill, experience, availability, geographical location, and other variables.
An hourly wage for skilled woodworkers is between $20 and $50.
A less skilled woodworker might charge as low as $10 per hour.
Where can I find free woodworking plan?
To find free woodworking plans, you don't have to buy any magazines or books. All you need to do is search Google. Just enter "free woodworking" into the search bar, and you'll see hundreds of websites where you can download free plans.
What is the minimum investment a hobbyist needs to make in order to get started?
A lot of capital is required to purchase the necessary supplies and tools if you want to start your own woodworking shop. The best place to start is by buying a small drill press, circularsaw, circular saw or sanding machine. These items are affordable so you won’t break the bank.
Statistics
- Most woodworkers agree that lumber moisture needs to be under 10% for building furniture. (woodandshop.com)
- Average lumber prices rose about 600 percent between April 2020 and May 2021. (familyhandyman.com)
- If your lumber isn't as dry as you would like when you purchase it (over 22% in Glen Huey's opinion…probably over 10-15% in my opinion), then it's a good idea to let it acclimate to your workshop for a couple of weeks. (woodandshop.com)
- In 2014, there were just over 237,000 jobs for all woodworkers, with other wood product manufacturing employing 23 percent; wood kitchen cabinets and countertop manufacturing employing 21 percent. (theartcareerproject.com)
External Links
How To
How to drive a nail through wood
It is essential to pick the right size and style of hammer before you can drive a nail in wood. The most common types of hammers are claw hammers, sledgehammers, mallets, ball peen hammers, and hatchets. Each type of hammer has its pros and cons. A claw hammer works well when you're trying to hit nails with a heavy hammer. However it is difficult to precisely control where the blow hits. Although a sledgehammer can be used to hit large areas quickly, it is too heavy to be useful for small tasks.
After choosing the right hammer, place your hand flat against the side of the head so that the handle rests comfortably in your palm. Hold the handle in your hand, but don’t force it too hard that you break. Keep your wrist relaxed and the hammer straight up. Now, move the hammer towards the center of the nail by swinging it back. The impact of the hammer hitting the nail should be felt. You can practice swinging the hammer with a block or wood until you feel the rhythm.
Once you are ready to drive the nail, place the hammer close to your body. The nail should be perpendicular to wood's surface. Keep your eyes focused directly on the tip of the nail. Swing your hammer forward. Then follow through with the motions of the hammerhead. Repeat this action several times, gradually increasing the speed of the swing. Try adding power to your swings when you've mastered the technique. Then, raise the hammer from your shoulder to bring it down. You'll have more energy to work with.
After you have nailed the hole, take the hammer off the nail. To pull out the remaining nails, use a screwdriver or pry bar. Keep the nail heads parallel to the board's surfaces in order to avoid splitting wood.