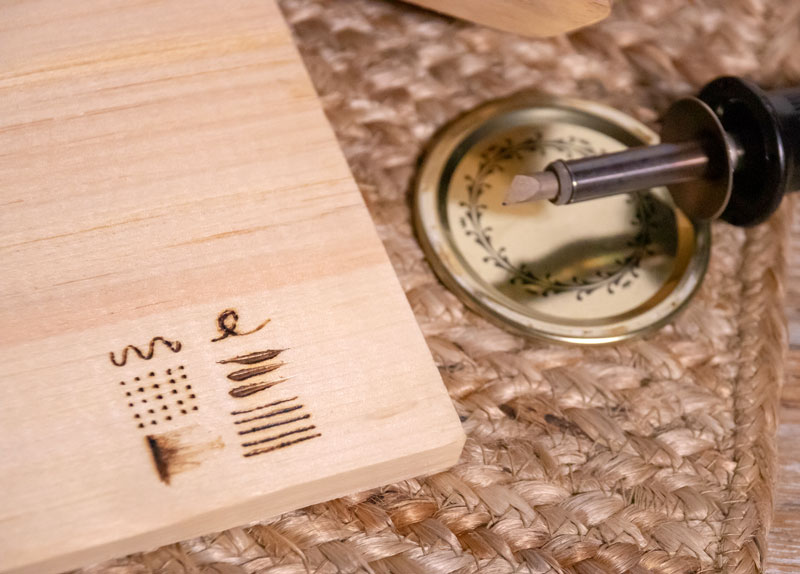
If you are looking to create beautiful and custom pieces for home, you might be interested learning more about pyrography. This ancient art involves the burning of intricate designs and ornaments into wood. It dates back to 17th century. The result is beautiful burn marks that create dark designs. These can include landscapes or portraits. This technique has been in use for centuries and is still a popular choice when it comes to home decor.
Yoko sugi ban
A technique called shou sugiban was used in 18th-century Japan to preserve wood by charring its surface. This creates a rich charcoal-black color on the wood's exterior, which can also give it an Alligator skin or cracked appearance. The Japanese cedar is the most popular wood for its rustic, traditional look. However, other wood species can be used with different degrees of success. The wood will be protected from future damage through controlled charring. This is an excellent preservation technique.
Shau sugi ban
The way char is removed is the main difference between shou suugi ban and traditional sanding. Some woodworkers using shou-sugi ban use wire brushes to remove the charred top layer, while others use coarser sandpaper. You want to remove enough char to expose the brownish-black color below. You will see a pattern that resembles an alligator skin. To remove excess char, sanding is required.
Shau sugi ban on cedar
While shou sugi ban on pyrography creates an appealing wood finish, it has practical implications. People can inhale bits of charred timber and track them throughout buildings. In order to address this issue, pyrographers now use a propane torch as an alternative to traditional wood-burning. Here's a comparison of these styles.
Yakisugi ban on bassewood
A centuries-old Japanese technique, yakisugi ban on cedar, can add beauty and durability to wood. This process, sometimes called Shou sugi ba, involves charring wood's surface to create beautiful patterns. The practice is so widespread in Japan that cedar has been used in many shousugi ban projects. In this article, operations director of a Japanese woodworking company, Satoshi Kimura, explains why shou sugi ban is so popular and what it means to woodworkers.
Yakisugi bans blue stain pine
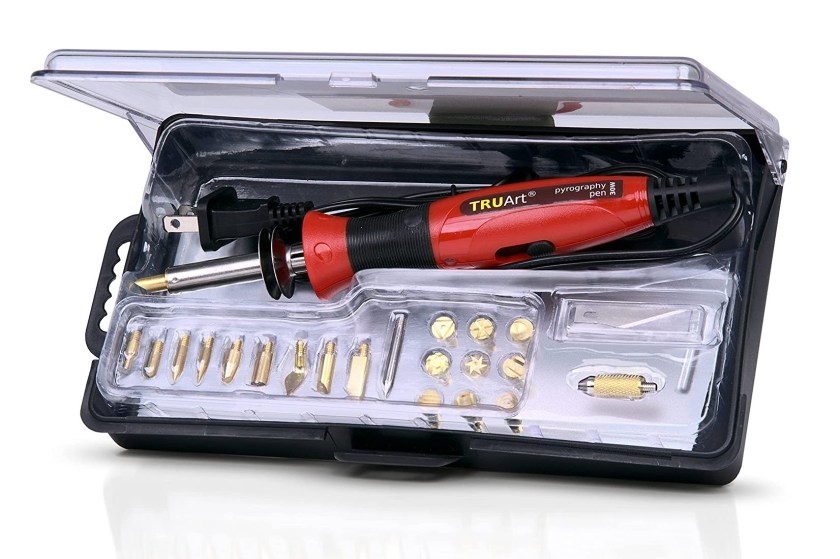
This process, commonly referred to as shou sugi ban, uses fire to preserve wood. Traditionally, cedar is used to perform shousugi ban. But other woods can also be used. Although cedar is the preferred wood for this method, yakisugi could be applied to maple, oak, or birch. The technique is particularly popular among traditional Japanese craftspeople.
Shau sugi ban on basswood
Charring cedar creates a deep black, rich color and crackled surface. Cedar is naturally resistant and repels bugs. However, the surface that has been charred can be used to shape wood. Untreated and reclaimed wood are available. Alternatively, a cedar panel can be treated to produce a more subtle burnt wood finish.
Shau sugi ban on jelutong
There are several benefits to shou sugi ban on pyrography on wood. The technique improves wood's natural patterns. Charred wood is also more durable due to the thicker carbon layer. It all depends on the wood species used and the environment it is placed in. Shou sugi ban can be an eco-friendly option to treatment wood.
FAQ
What's the difference?
Hobbyists are passionate about making things from wood, while professionals tend to be more focused on the quality and craftsmanship of their work. Hobbyists often take pride in the creations they make and often share them to family and friends. Before they start working on a project, professionals will spend hours researching the designs. Professionals will be meticulous about all aspects of their work, from selecting the right materials to finishing it.
Are there any tips for starting a woodworking enterprise?
Starting a woodworking business is a lot of work. You won't mind working hard if your hobby is something you love. You will probably love the challenge of starting your own business.
Remember that you may encounter unexpected problems when starting a new venture. You might run out money, or you may have to borrow unexpectedly. Maybe customers won't be willing to pay what you want. These situations are necessary for survival.
It is a good idea to create a separate bank account just for your company. This will ensure that you always know how much money has come in.
What woods are suitable for making furniture?
Woods are classified according to their hardness. Softwoods can be pine, fir or cedar. Because they are resistant to rot, softwoods are often used as outdoor furniture. These hardwoods include maple, mahogany and teak. Because they can't weather outside, they're usually used indoors.
What wood items do well?
Wood that has been harvested sustainably is the best-selling type of wood.
Oak, cherry and mahogany are the most sought-after wood types for furniture.
These woods are extremely strong but also have beautiful colors and grain patterns. They also last for many years if cared for properly.
To prevent moisture damage to wood furniture, it is important that it be painted before any other surfaces. This applies to all surfaces, even drawers and doors.
You want your furniture to last as long as possible so you need to choose a paint that is water resistant.
Use a high-quality, oil-based primer and two coats of topcoat. Depending on how much wear you expect, you might need to apply more coats of topcoat.
Avoid spray cans and aerosol paints. These products can evaporate quickly and emit harmful fumes.
What would you recommend as a starting material for woodworking?
You can start with softwoods like pine or poplar. After you are comfortable with the softwoods, move to hardwood.
Statistics
- In 2014, there were just over 237,000 jobs for all woodworkers, with other wood product manufacturing employing 23 percent; wood kitchen cabinets and countertop manufacturing employing 21 percent. (theartcareerproject.com)
- The U.S. Bureau of Labor Statistics (BLS) estimates that the number of jobs for woodworkers will decline by 4% between 2019 and 2029. (indeed.com)
- Average lumber prices rose about 600 percent between April 2020 and May 2021. (familyhandyman.com)
- Woodworkers on the lower end of that spectrum, the bottom 10% to be exact, make roughly $24,000 a year, while the top 10% makes $108,000. (zippia.com)
External Links
How To
How to make wooden joints
This tutorial will show you how to join two pieces of wood together. The "pocket hole joint" is a method whereby we drill holes into the wood and glue them together. If your wood has a straight grain, smooth surface, you can use this method. You might consider dowel joinery if your wood isn’t straight or flat. These are the steps
-
Drill Pocket Hole Joints. First, measure the area where you wish to place the pocket joint. Then drill 3/4 inch deep holes into the ends of each piece of wood using a jig saw or handheld drilling machine.
-
Sand Smooth. Sanding the edges of the wood will help to prevent the joint from splitting later.
-
Glue both sides together. Apply glue to the sides of both wood. Let it sit for about 5 minutes before clamping the pieces together.
-
Clamp the Pieces Together. Once the glue has dried, clamp the pieces together so they are flush.
-
Trim Joinery. Trimming the joinery after glue has completely dried.
Make sure to leave enough room between the pieces so that you can turn them inside and out.